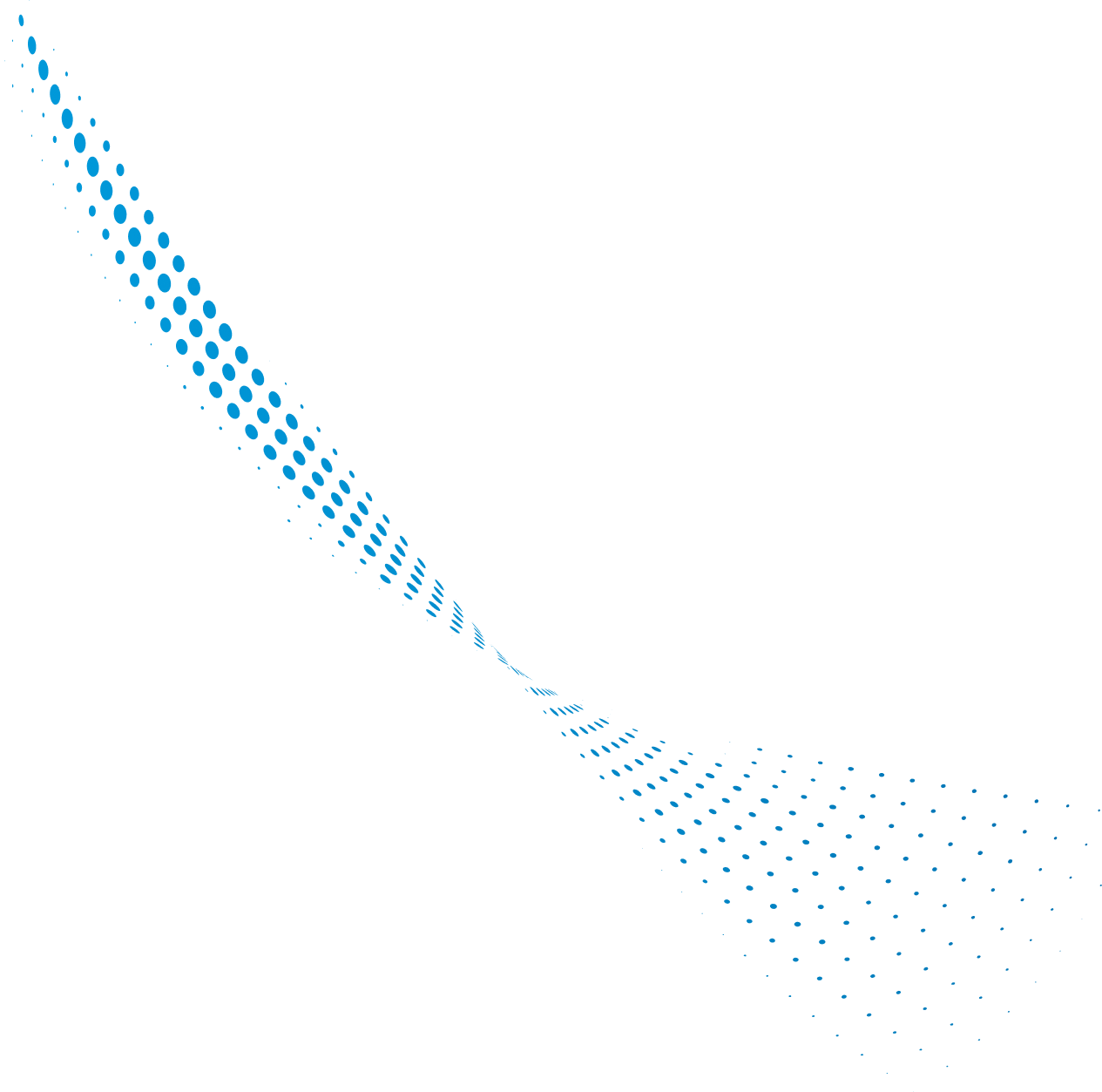
Want our experts to contact you?
Reimagining Production
Expanding manufacturing capacity represents the quintessential opportunity to innovate. A greenfield facility allows stakeholders to rethink how the business will approach production, how it will interact with people and the environment, and what to prioritize to support long-term growth. Unconstrained by the status quo, greenfield planners can reimagine production logistics using leading-edge digital technologies to identify solutions to today’s manufacturing challenges.
Applying lessons learned and successes from existing manufacturing sites has merit, and duplicating a facility has the advantages of economy and expediency. However, compared to today’s standards and expectations, productivity and corporate objectives are different than when the legacy facility was built. The sustainability, flexibility and resilience required now might not have been a top-level priority back then. Digital transformation and technologies such as artificial intelligence (AI), augmented reality (AR), and machine learning (ML) were not as advanced as they are now. Missing the opportunity to innovate on a new or expanded capacity project can cost the business dearly in terms of total cost of ownership (TCO), return on investment (ROI) and competitive advantage.
As technology rapidly evolves, the challenge is identifying the right opportunities and technologies. After a project team clearly defines company objectives and considers all relevant corporate initiatives, they can focus on three primary areas – autonomous operations, sustainability, and AI – to help provide a framework for a more detailed planning phase.
- Autonomous Operations
The ideal scenario for any modern manufacturing facility is to reach fully autonomous operations. The level of autonomy in a planned greenfield facility is higher or lower, depending on the industry. For example, warehousing and automotive manufacturing can be highly automated and able to operate with little or no human intervention (“lights out”). Many high-precision, small batch industries like life sciences, dairy, baggage handling, clothing, and high-tech electronics, however, have a lower level of autonomy.
The automation of every manufacturing process or hyperautomation allows manufacturers to reduce operational error, increase quality and control costs more efficiently. Hyperautomation also mitigates the impact of the industrial workforce shortage and applies human effort to more strategic tasks rather than low-skill or low-value tasks like material movement.
A world-class automation solutions provider can team with internal stakeholders to evaluate product movement through a potential greenfield or new capacity facility. They can digitally assess production logistics, product changeovers and process and asset optimization. After this assessment is complete, a thoughtful and thorough design is configured for an open, software-defined architecture that provides safer and more secure operations. The right design techniques offer scalable, flexible, and modular facility plans that simplify complex processes and streamline production using the right mix of robotics, AI, and ML.
- Artificial Intelligence
AI and real-time ML are the hallmarks of digital transformation and modern manufacturing. A connected enterprise uses data streams from production control, smart devices, logistics and edge and cloud information systems to feed the right insights and information to people who can then make knowledge-enabled decisions to support business growth. AI can push data and insights to the right places in the enterprise to support operators, users, and management.
Generative AI and ML identify hidden patterns and provide statistical relationships and responses to operational situations without human intervention. Digital technology allows machines to take in information and draw certain conclusions. As a machine learns, it adapts and becomes more intelligent over time. Historical knowledge can also be programmed into the system to take advantage of human insights that previously served the operational side of the process well.
Advancements in ML have enabled true closed-loop optimization. Closed loop implies the equipment and process will self-regulate and be the most efficient and productive or find the right balance without continuous human intervention.
- Sustainability: Energy Management
A challenging priority for manufacturers is to invest in ongoing sustainability initiatives while also trying to achieve productivity and profitability targets. In the quest for green manufacturing, manufacturers want to become carbon neutral or carbon negative to reduce the impact on the environment and stay in compliance with tightening regulations. They must first optimize energy usage to lower overall demand and supplement that demand with new, cleaner energy sources that are more eco-friendly, such as hydrogen, solar, wind and biofuels. Finding the right combination of energy sources requires contextualized data from both energy management and production systems.
Reviewing production and energy data helps reveal insights into the complex relationship between each product and related energy costs. In traditional manufacturing, companies review the overall process and consider raw materials, labor and overhead when calculating product costs. Overhead, including the cost of keeping the entire facility operating (e.g., energy, wages, salaries, and maintenance), might be evenly weighted among all products as a percentage of the overall facility cost. With today’s unprecedented access to data from every aspect of plant-floor processes and equipment, including devices, resources, inventory, and more, a broader picture is possible, revealing specific opportunities for efficiency and productivity.
Data insights from AI are pushed to operators and end users to support decision-making that enables both sustainability and productivity. Knowledge-driven decisions can refine production strategy to optimize assets, productivity and energy use. Design changes, consumer preference, changing energy costs and production run variations all affect the type and quantity of energy needed to minimize cost and environmental impact while maximizing productivity.
When considering product costs, AI-powered analytics provide data on resources used. For example, it can show the energy type, when it was purchased or generated, and at what cost or time of day. Inferences can be drawn as to how to lower the cost or change the product to use less energy. Workers can analyze and apply contextualized data to one product across multiple production runs to ascertain patterns, inefficiencies, raw materials problems, or other issues. They can then make real-time, data-driven decisions to optimize performance and efficiency throughout plant processes.
Boldly Go.
Innovation is ongoing, especially as rapidly evolving technological advancements challenge facilities to stay up to date. Support after a greenfield project is key to continuous improvement and optimization, as are future upgrades and modifications to safeguard the original investment. Partner with a team who is already familiar with the facility’s systems. A team that can draw from tech-savvy resources who have the industry knowledge and expertise to provide fast local and global support.
Technology continues to move us deeper into a digital world, one that spills over into the physical world more every day. Remaining in an innovative mode and staying agile will help manufacturers sustain greenfield – and brownfield – facilities.
Greenfield projects require a digital mindset. Don’t settle for what has already been done. Put the traditional approach on hold, question assumptions and discover what is possible.
What’s Next?
Upfront consulting with a well-rounded, reliable, and knowledgeable automation solutions provider is well worth the time and effort in helping to put the new facility online and to facilitate continual optimization.
Rockwell Automation offers solutions:
Contact us to learn more about how we can help you innovate on your new or expanded capacity projects.